CIRCOR Operating System

Achieving operational excellence means focusing on continuous improvement through processes that are repeatable, reliable, and Lean. At CIRCOR, we embrace this approach through our own comprehensive program—the CIRCOR Operating System (COS).
COS aligns people, processes, and technology to empower our employees, making continuous improvement part of the daily experience. It focuses on results-driven leadership; the elimination of waste (cost, time, quality, resource, space); Lean and process controls for speed, flexibility, and efficiency; higher performance for greater market share; and the improvement of cash flow through inventory reduction or increased turns.
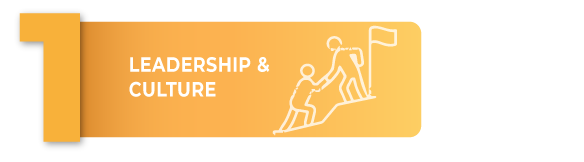
Eliminating manufacturing waste and non-value added processes, Lean helps ensure the delivery of quality products on-time, all the time.
- Elimination of Eight Deadly Wastes
- Visual Factory/Andon
- Model Cell Design/Continuous Flow
- Value Stream Mapping/Standard Work
- Lineback Logistics/Replenishment
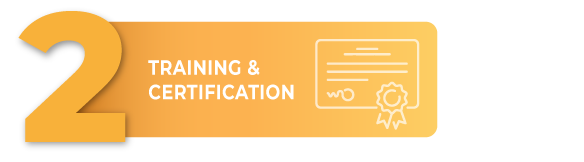
Developing skills is critical to achieving organizational effectiveness and operational excellence. These programs define proficiencies and expectations for all employees.
- Skills Assessment Matrix
- Job Classification & Certifications
- Training Courses Conducted
- Awareness, Practitioner, Master Levels
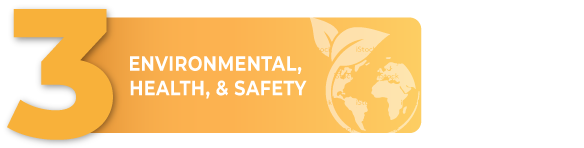
To improve EH&S standards and culture, employees are trained to proactively manage all types of risks, offer proactive suggestions, and own decisions.
- Safety Program & Culture
- Management & Audits
- Sustainable Practices
- Employee Engagement & Risk Surveys
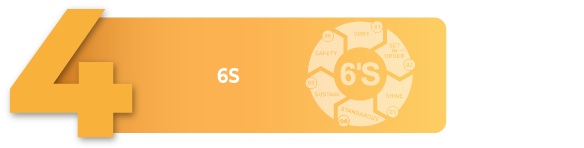
Sort, Straighten, Shine, Standardize, Sustain, Safety—this is our process for organizing and sustaining a clean, safe, high-performance workplace.
- Work Area Safety & Ergonomics
- Foreign Object Damage Controls
- Material Packaging & Handling
- Tool Control & Shadow Boxing
- Daily Checklists & Audits
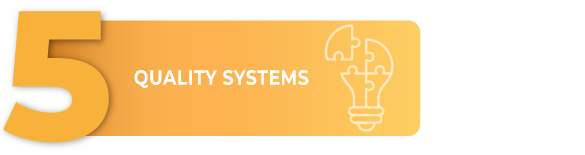
Our Problem Solving Centers of Excellence diagnose problems, perform root-cause analyses, and apply solutions to any process inefficiencies. Actions are carefully monitored for accelerated learning.
- Turnback Reduction
- Standard Problem Solving 10 Steps
- Quality Clinics
- Mistake Proof Solutions
- Corrective Actions Effectiveness/Read Across
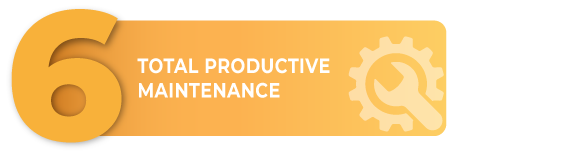
Our proactive method for achieving maximum equipment effectiveness through employee involvement covers manufacturing, support equipment, or office equipment.
- Daily Weekly/Monthly Equipment Maintenance Logs
- Operator Daily Walk-Arounds
- Overall Equipment Effectiveness
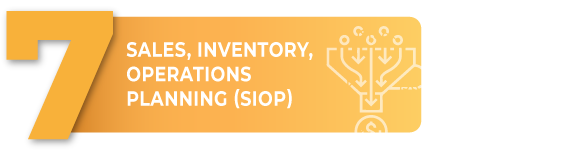
This monthly process aligns production, demand, and financials through a sequential four-week planning process.
- Standard Work
- Demand Planning
- Supply & Capacity Planning
- Pre & Executive SIOP Reviews
- Key Process Indicators Dashboard
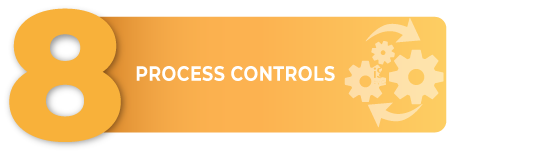
A variability-reduction strategy that integrates teams, tools, and techniques for to achieve turnback and defect-free processes and products throughout the entire value stream.
- Change Management
- Production Control Plans
- Statistical Process Controls
- Business Process Controls
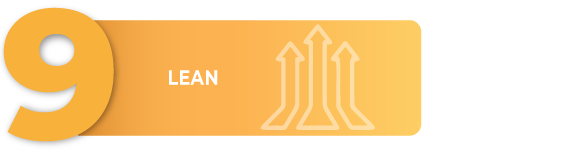
Eliminating manufacturing waste and non-value added processes, Lean helps ensure the delivery of quality products on-time, all the time.
- Elimination of Eight Deadly Wastes
- Visual Factory/Andon
- Model Cell Design/Continuous Flow
- Value Stream Mapping/Standard Work
- Lineback Logistics/Replenishment
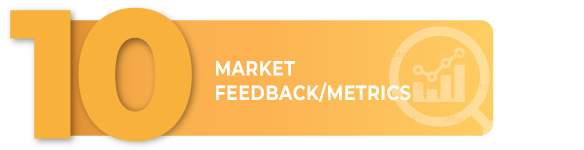
During monthly Management Review meetings, leadership compares business metrics to goals, targeting areas needing improvement or resource deployment.
- Customer Scorecard
- Compliance & Controls
- Corrective Action Boards/Rolling Action Item Lists
- Gap Closure Plans/Maturity Progression